Industry Talk
Regular Industry Development Updates, Opinions and Talking Points relating to Manufacturing, the Supply Chain and Logistics.UK Manufacturing: The Productivity Conundrum
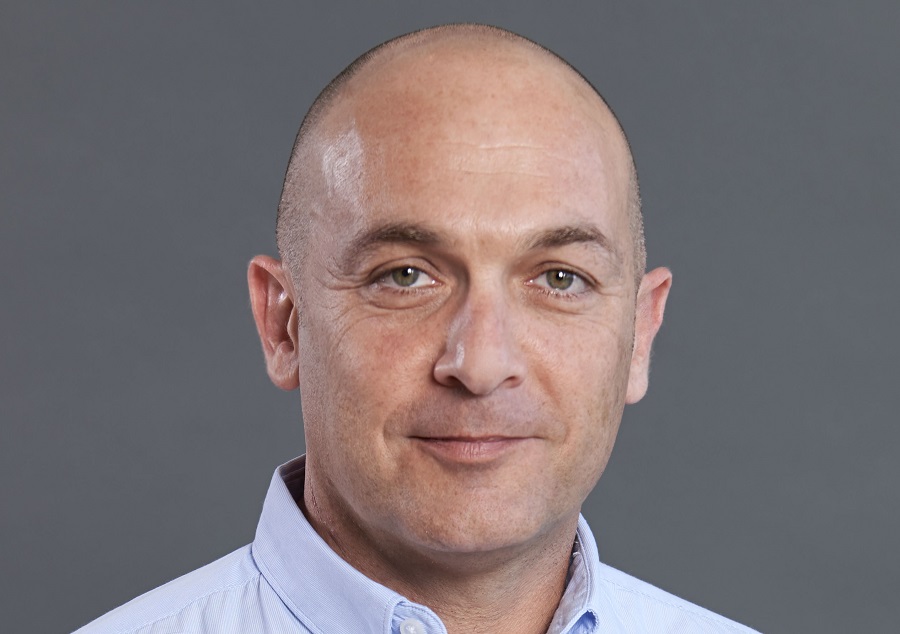
The Conundrum
Manufacturing has long been a central pillar of the UK economy, consistently delivering quality and innovation. However, it’s currently suffering a from a dip in productivity levels, in line with the rest of the UK.
The manufacturing industry has been hit harder by the productivity slump than most. Summer 2018 saw output and new orders slow down, and the first contraction in the export business since 2016, according to an IHS PMI report. The report showed August had the slowest rise in manufacturing production in 17 months, and new manufacturing orders eased to its lowest in 25 months.
It also appears that the UK is experiencing a perception problem surrounding the efficiency of the manufacturing and supply chain. According to recent research, there is a serious disparity between perceived and actual productivity amongst business leaders in manufacturing. Findings showed that over 80 per cent rate stock checking, collaborating on cross-departmental projects and submitting expenses as efficient, yet 85 per cent also admit to wasting up to 10 hours per week on administrative tasks. So, what’s causing these misconceptions?
The Workforce
According to the Chartered Institute for Personnel and Development, the decline in UK-wide efficiency is driven by poor management practices, and insufficient investment in upskilling staff. The level of investment and ambition, they say, “particularly relating to skills and how they are used in the workplace, is inadequate, given the scale of the productivity challenge facing the UK.”
Indeed, research showed that 33 per cent of manufacturing business leaders would spend more time on personal training if they could, whereas only 24 per cent would spend more time on training of their team. Similarly, 41 per cent said they would spend more time on strategy and planning, and only 28 per cent on team-building exercises.
These numbers suggest business leaders might be forgetting the importance of upskilling the supply chain workforce, which could be symptomatic of a disconnect between how management and employees perceive productivity. In many cases, employee perspectives more closely reflect the reality of the situation. After all, employees are likely to have a better idea of their own productivity, and whether they’re equipped with the right tools to get the job done.
Business leaders need to look to the needs of the workforce to understand what’s needed for the job at hand. Equipping the workforce with the right tools will help to boost productivity, and also bolster satisfaction levels, which are equally important. It’s not just about blindly throwing money at the problem, but rather redirecting funds towards building a productive workforce, and steering clear of loose management practices where possible.
The Technological Tools
Another factor taking a toll on supply chain productivity is the reliance on outdated legacy systems, or in some cases, no business management systems at all. Not only is this negatively impacting productivity, but it’s also costing UK businesses billions.
The attachment to restrictive spreadsheets and inflexible systems means that manufacturers are missing out on real-time assessment and reporting, alerts on bottlenecks and preventive operations, and a secure platform to store their data. Thankfully, this is an issue easily remedied by updating technological arsenals with the latest cloud-based business management solutions, such as ERP or CRM.
One of the biggest challenges for organisations today is that the outdated technologies that underpin their data processes have not been designed for today’s multichannel digital world. With the rise of the IIoT (Industrial Internet of Things), connected devices are generating vast quantities of data that legacy systems aren’t equipped to house or interpret. Industry 4.0, the adoption of interconnected systems that change the way organisations and systems interact, is already here, and manufacturers risk being left behind.
Digital transformation is no longer a choice; it’s a process all firms must go through to stay competitive and to ensure their data is secure. So, given the risks, why aren’t decision makers quicker to drive technological change? Some are worried about the cost of digital transformation and potential system downtime, and others fear the transition from on-premise data servers to cloud-based storage or maintaining business continuity when working from mobile devices. These concerns are easily addressed, though, by a carefully considered and strategic approach to digital transformation.
Research revealed that 70 per cent of C-level executives in manufacturing spend 5-10 hours per week on administrative tasks, a number easily reduced just by having the right technology in place. UK manufacturers must embrace the latest technological advances or risk low productivity levels and reduced revenue, which will be infinitely more damaging to the business in the long-run.
Conclusion
With UK industry at a crossroads ahead of an exit from the EU, the importance of productivity has been further amplified. According to findings, senior decision makers are widely overestimating productivity, and neglecting the importance of upskilling their workforce and embracing new technologies. So, in short, to unpick the productivity conundrum manufacturers must also build a work culture where real-time, transparent communication up and down the supply chain is at the core of the organisation, and where technology is a celebrated facilitator.