Industry Talk
Regular Industry Development Updates, Opinions and Talking Points relating to Manufacturing, the Supply Chain and Logistics.Managing a Supply Chain during COVID-19: What can we learn?
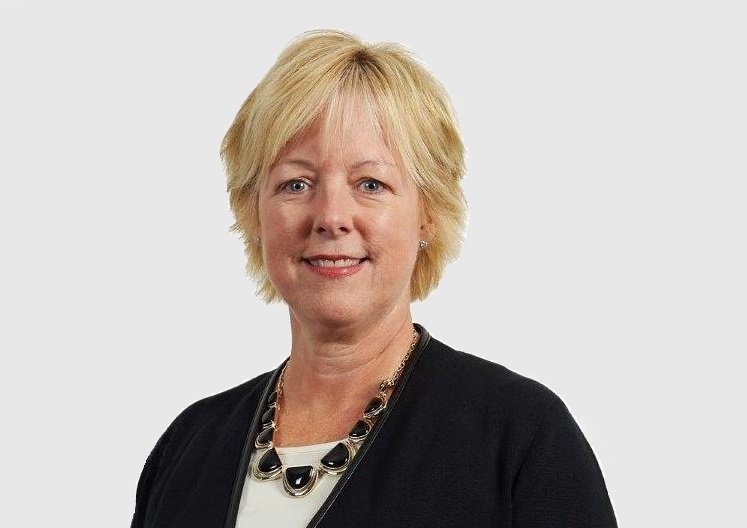
Striving for flexibility in a supply chain is not a new phenomenon. For years, managers have looked to supply chain flexibility to help minimise the risk of disruption during more difficult times, while also reducing the wastage in their processes.
However, the COVID-19 pandemic has created risks and challenges far beyond those that we have experienced before, with its effects having a huge impact on a wide range of industries.
With businesses now operating in a global market, supply chains have increased in complexity. Production and manufacturing are now frequently offshored in order for companies to gain the benefit of reduced costs. However, as a result, goods must now travel significant distances in order to reach their final destination.
In March, near the beginning of the pandemic, 75% of companies reported supply chain disruptions due to transport restrictions introduced to manage the spread of COVID-19, according to a study by the Institute for Supply Chain Management. As a result, this highlights the importance for companies to have a flexible and robust supply chain that is geared up to deal with unpredictability.
Debbie Lentz, President of Global Supply Chain at RS Components and the Electrocomponents Group discusses why building a resilient supply chain is key to delivering products and services successfully, and the lessons learned about operating global supply chains in the wake of the COVID-19 pandemic.
Resilience is key for supply chain success
It is crucial for businesses to ensure that their supply chains are resilient – by doing so, operations will run more smoothly and will be able to withstand even the most unpredictable circumstances without significant delays.
According to a survey by the Institute for Supply Chain Management, more than 50% of companies included experienced sudden and unexpected delays in receiving orders at the start of the pandemic, with half of the companies also lacking any contingency plans that could be implemented in the event of supply chain disruptions leading back to China. Although work-in-progress, delays and inventories across the supply chain can be minimised by just-in-time and lean manufacturing, at the other end, any disruptions will be quickly felt throughout the chain.
Speaking on the subject Debbie adds:
“With McKinsey estimating around $5 trillion in losses due to the supply chain shocks that have occurred as a result of the COVID-19 pandemic, supply chain disruption can be very costly. Businesses that rely on a sole supplier could realistically see a total loss of production almost overnight, so developing a diverse range of suppliers is paramount.
Although developing additional paths for the flow of goods can come with additional costs, the benefits that will be seen during difficult times – and the ability to adapt quickly as problems arise – are worth the investment. Regional supply chains can be expensive, but they help to reduce geographic dependence and shorten delivery times, as well as the need to transport goods across wide or fragmented geographic areas. As a result, any disruptions to international transportation will have much less impact on the supply chain, as products will already be closer to the end consumer.”
Leadership teams make impact by mitigating risk
Whilst there is always a level of risk within any business setting, if a leader fails to identify and mitigate risk, there can be a serious and significant impact.
Leadership teams must ensure that they are in a position where they have the ability to analyse data to drive efficiencies in their supply chain. In doing so, they can also spot and intervene with any blockers in the process, as they are the key decision-makers. Although none of us have ever experienced a global event like the COVID-19 pandemic, the warning signs that supply chains will see significant disruption were present from the outset. Leaders should have the ability to anticipate potential issues and make preparations before these situations become critical by maintaining a high level of awareness of the environments in which they are operating.
Debbie advises:
“A large part of being a good leader is the ability to be proactive, by getting ahead of any problems before they arise. This is where data really comes into play, as really understanding the operational details can help you understand where there may be potential risks. Prevention is key – for example, implementing actions to a given situation before any negative impact can occur on quality and delivery. By being alert and giving due consideration to all situations, no matter how unlikely they may seem, a lot of time, money and worry can be saved further down the line.”
Utilising technology
COVID-19 has emphasised the critical importance of resilience for businesses around the world. However, technology, when implemented effectively, can aid businesses in anticipating problems in their supply chain and help them to react quickly to minimise disruption – especially when stages of the chain are spread across the globe. As a result, there has been significant demand for companies offering these services, with one Munich-based company seeing requests for trials of their software up 200% from one year ago.
Digitalisation can help to improve efficiencies within the supply chain in a number of ways, with digital twin systems just one example of this. Digital twin systems are able to find alternative routes, production methods, and suppliers for a supply chain, with the highly accurate plans able to be implemented almost immediately in the case of any disruption. AI technologies are also able to provide managers with deeper operational insights and accurate forecasts, by gathering and analysing current and historical data from a range of sources.
As such, AI solutions can help decision-makers to hone in on the best routes and easily identify any bottlenecks in the chain, enabling them to reduce time and overall cost of warehousing and shipping during the process.
Debbie continues:
“Artificial intelligence is a very useful tool because of the invaluable insights that it can provide based on historical and forecasted data, which can help when assessing possible vulnerabilities in a supply chain and in some cases, also spotting solutions to issues that do arise. However, although these technologies have their place in our processes, being proactive, using data to predict future trends and being able to apply these trends are most important.
The environments in which businesses are operating have seen a near-constant stream of significant changes as a result of the unpredictable circumstances created by COVID-19 this year. However, as we move towards a new normal way of working, it is without doubt that ensuring supply chains are robust and flexible is at the forefront of the mind for many, so that any similar challenges can be faced head-on if they arise in the future.