Industry Talk
Regular Industry Development Updates, Opinions and Talking Points relating to Manufacturing, the Supply Chain and Logistics.Eight Ways Companies are Shifting Operations of Core Products Due to COVID-19
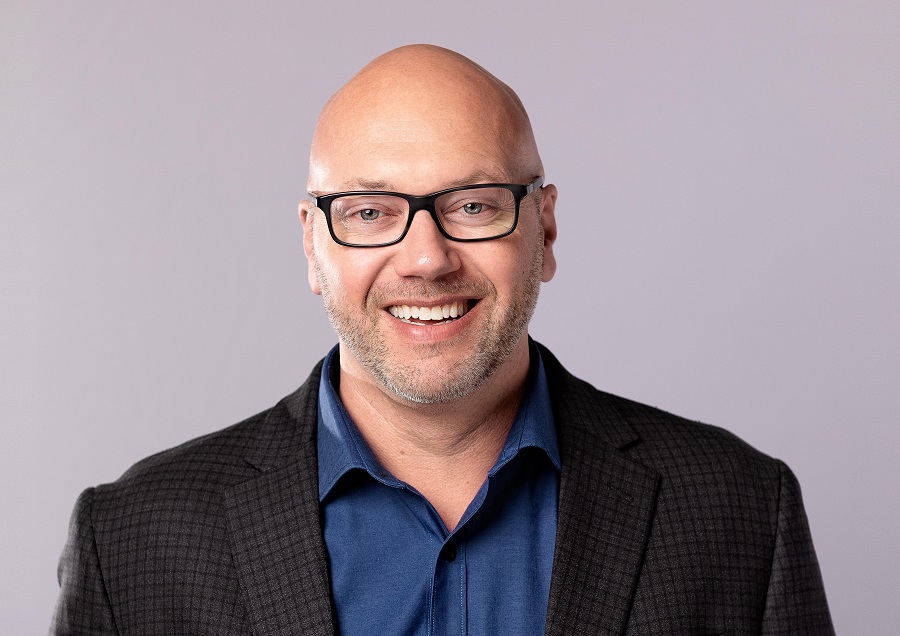
Customer demand patterns have dramatically shifted due to the widespread quarantines that were instituted by top government officials. Finely tuned supply chain planning systems were suddenly not able to effectively manage the onslaught of changing patterns. Entire product lines ground to a halt while others soared at never anticipated or believed rates as e-commerce went viral. To effectively cope with these sudden shifts in demands, companies have adopted a host of techniques to realign their supply chains with the needs of the market. Below are seven key strategies that are proving to be successful.
- Leveraging AI to Forecast New Trends: Historical trend data that relies on seasonality from past years selling seasons is, in many cases, no longer valid. Companies are leveraging new applications that utilize AI, external COVID-19 causal data, and the power of cloud compute to churn through daily sales data quickly. They can detect rapidly shifting patterns, forecast demand volumes with machine learning algorithms, and display those insights with predictive analytics.
- SKU Pruning to Increase Production Line Capacity: Manufacturing organizations are assessing their product category exposure. They are eliminating entire product lines of slow-moving items freeing up manufacturing capacity for critical surge items. Even for those surge items, it is becoming commonplace to reduce packaging sizes so that lines have less downtime and thus have a better chance of keeping up with demand.
- AI-Powered Advanced Analytics for Determining Safety Stocks: Safety stocks are on the rise due to increasingly erratic demand patterns, unforeseen supply interruptions due to COVID outbreaks, and changes in maritime practices. It is now commonplace for countries to allow pilots to board incoming vessels at their destination port only after 14 days have passed since leaving their origin port. Ships with travel durations less than 14 days are required to anchor and complete what is remaining of a 14-day self-isolation period before a pilot will be allowed to board and help to dock the ship. If any crew member comes down with COVID-19 like symptoms, the vessel will not be permitted to dock until all the crew members have been symptom-free for 14 days. This increase in ocean transit times is causing replenishment times to lengthen and is necessitating an increase in safety stocks.
- Harnessing Core Competencies: Closed factories are deploying their vast engineering talents to quickly retool lines and develop processes to ensure that critical goods keep flowing to the market. One global apparel retailer quickly retooled a manufacturing location in Massachusetts to sew and manufacture washable fabric masks that are being used by the nation’s logistics workers within critical infrastructure positions.
- Data Science War Rooms – LLamasoft is providing SWAT teams consisting of data engineers, data scientists, and supply chain modeling experts to stand up applications in a matter of days and weeks to help organizations rapidly harness the power of AI to make driven decisions on how to effectively utilize supply chain capacity for alternative products (https://llamasoft.com/war-room/)
- Collaboration in a Safe Space – Executive committees for various supply chain conferences have formed COVID-19 task forces where they discuss challenges and solicit assistance from experts at other member companies. A large banking infrastructure company was able to leverage another company’s executive relationships with a global freight forwarding company to successfully secure airfreight transportation to move critical PPE materials out of China.
- Extending Relationships – A global manufacturer of medical equipment is relying on partners to help then during their surge in demand. In geographies around the world, they have contacted suppliers and customers who have idled workers and are re-employing them within their operations to increase throughput capacities. JD Logistics, one of the largest logistics providers within the Wuhan province and China, is partnering globally with LLamasoft’s other customers to provide extensive on-the-ground expertise and infrastructure to make sure that critical shipments happen in the quickest timeframe possible (https://llamasoft.com/jdlogistics-expedited-shipping-offer/)
- Manufacturing Shift Cohorts – Organizations are dividing their workforces into many groups of shift workers that can swap in and out for one another. If one person for any given shift becomes infected, then that entire team can be quarantined and swapped out with another team. This approach allows the assurance of continued production and keeps more employees engaged and contributing to recovery efforts.
Examples will grow as the manufacturing backbone of our country continues to deploy AI-based applications geared towards responding to the unique challenges brought forth by COVID-19.